Robot integration rear light assembly
The robotic measuring system places a rear light in the side frame of a vehicle body, after determining it via 3D scanning, in the best-fit position and holds it in place for further processing.
Robot integration rear light assembly
The robotic measuring system has the task of inserting a rear light into the side frame of a vehicle body in the best-fit position and holding it for screwing by the worker. The best-fit orientation describes the insertion of the rear lamp from the front position to the end position and the orientation at the joints of the given measurement points.
With the help of the robotic measuring, the robot grabs the rear light from a bracket and holds it in front of the 3D scanner. The 3D scanner determines the position of the lamp on the robot hand and the rear lamp pot. The robotic measuring moves the rear light to a pre-position in front of the car body. Based on the position of the rear light pot and the position of the rear light on the robot hand, a local correction step is calculated in order to be able to roughly insert the lamp into the rear light pot. Using laser sensors and a best-fit algorithm, the position of the luminaire is finely adjusted and optimized. The rear light can then be attached
By using force sensors, special tools and 3D scanners
The robotic measuring has various force sensors for gap and offset measurement. The robot removes the rear light from a defined location via its gripper system and positions it on the vehicle. The alignment takes place at the joints between stray glass and adjacent components. As soon as the end position is reached, a signal is sent for manual screwing.
Using this model, the positioning of a robot is to be evaluated as part of a pre-development project. The sensor and robot design must be designed for various derivatives; the rear light bracket and the rear body must be designed as interchangeable inserts. The rear light bracket must be screwed to the robot on a mounting plate. This plate must be designed for transport with a forklift. The learning of new derivatives using the same connection principle must already be implemented in the plant. The rear body includes the left and right sides of the vehicle to keep the option of installation on both sides by a second robot open.
In further project steps, the robot gripper should be able to pick up all rear lights that are installed on the assembly line. For this purpose, after detailed consultation, the AG must provide CAD models of the following derivatives, which are used as the basis for the construction of the gripper system:
The robot must be able to pick up these spreaders with the same gripper. If there are larger deviations, the gripper can have suction cups on different sides and use the correct holder by turning the gripper. The sensors must be selected and positioned on the robot in such a way that the derivatives listed above can be treated. The rear body must be mounted on a plate/bracket and designed to be interchangeable; the connection must be coordinated with the AG. The rear light holder can also be designed to be interchangeable.
Testing of robotic measuring to ensure quality and function
The measurement robots are specified and defined as a measurement reference in order to create a clear basis for decision-making for the final product evaluation and its approval.
Recognized and valued as a benchmark to meet the OEMs' and suppliers' acceptance scenario and to verify test results in accordance with contracted product specifications, with the aim of accepting the manufacturing quality of the product. Our factory standards and validations guarantee accurate product quality ratings, which are confirmed by our clients' auditors.
Quality assurance for global customers from the automotive, medical, aviation and lifestyle industries
The Battenberg Robotic Measuring is already being used by many OEMs and their suppliers as a standard and reference in quality assurance.
A wide range of global customers from the automotive, medical, aviation and lifestyle industries, such as BMW, VW, Audi, Ford, Daimler, Continental, Forvia, Hella, B. Braun, P&G and Lufthansa rely on the Battenberg Robotic Measuring. We export our robotic measuring systems worldwide and offer service and maintenance for them.
Benefits
- REPRODUCIBLE MEASUREMENT METHODS lead to validatable measurement results
- ECONOMICALLY thanks to modular, scalable expandability to many measurement tasks
- EASY TO USE via quick and easy graphical programming
- COST AND TIME SAVINGS through automation, simulation, and repeatability
- FLEXIBLE via parameterizable actions to program individual measurement processes
- VARIABLE in the exact orientation of the robotic measuring on complex test objects
Overview of all use cases
For over 40 years, we have been developing and supplying measurement robots for reliable quality testing of their products for our international customers. High-precision measurement, analysis and evaluation of product specifications and characteristics is required.
In the application, quality ratings and product approvals are carried out more securely and faster in the audit process, along with significant cost reductions and competitive advantages.
Overview of all industries
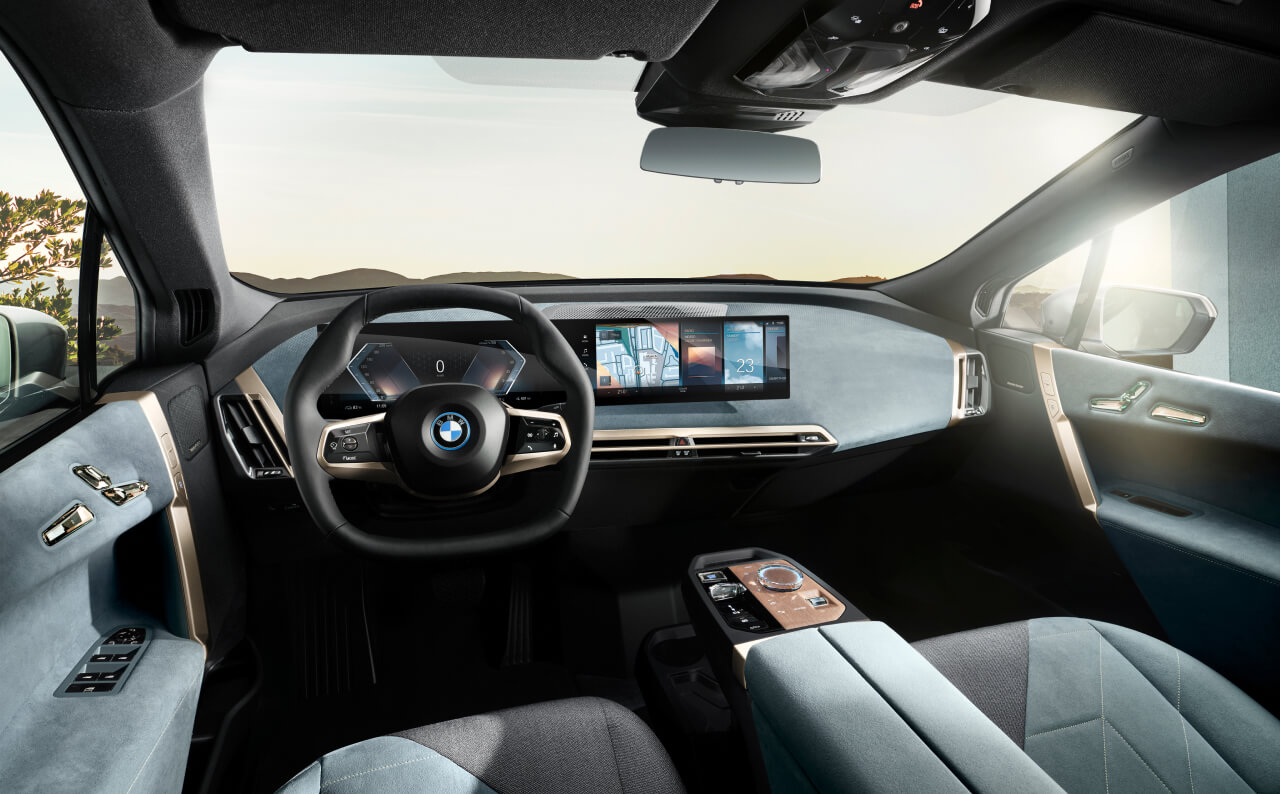
Automotive
Battenberg Robotic Measuring has been testing vehicle components in research, development, production and end-of-line assessments for over 40 years. The results are used for cause-effect analysis and quality improvement. The areas of application are determined by the requirements of the specifications, the test tasks and environmental conditions.
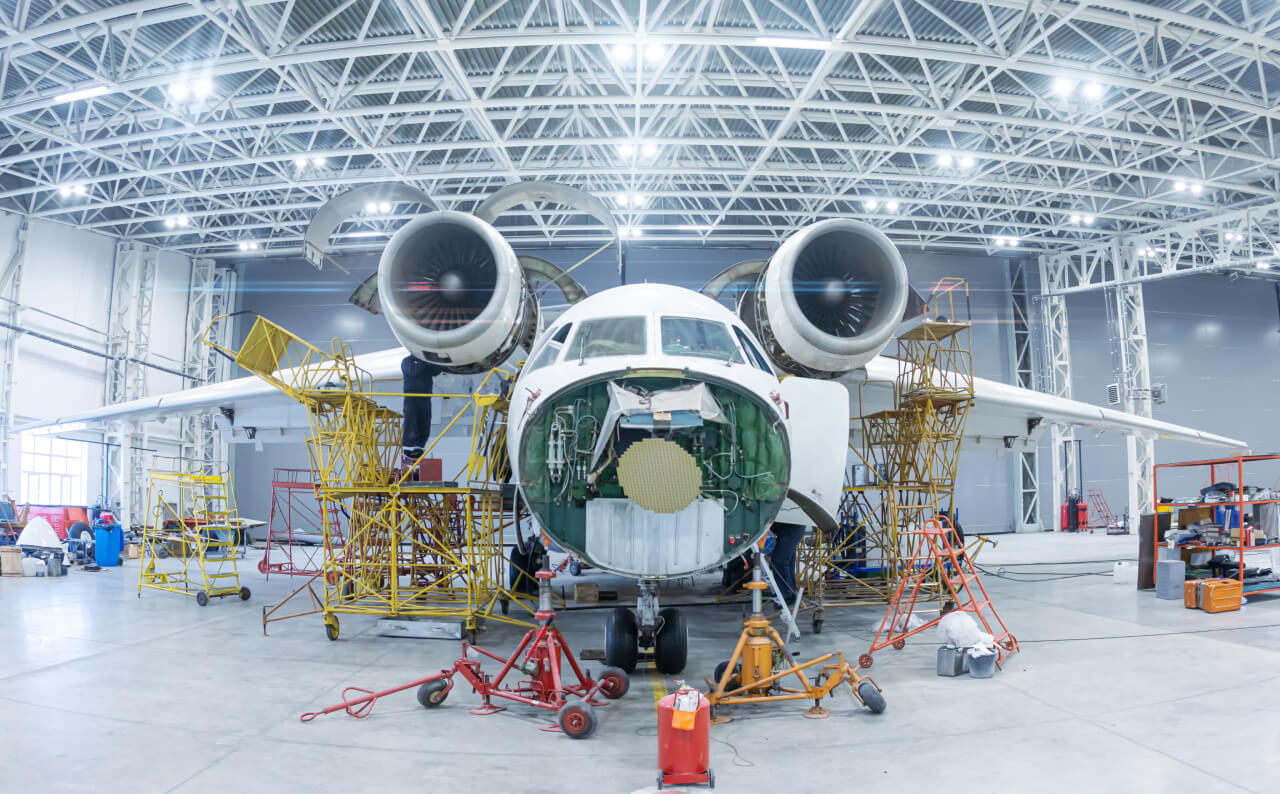
Aviation
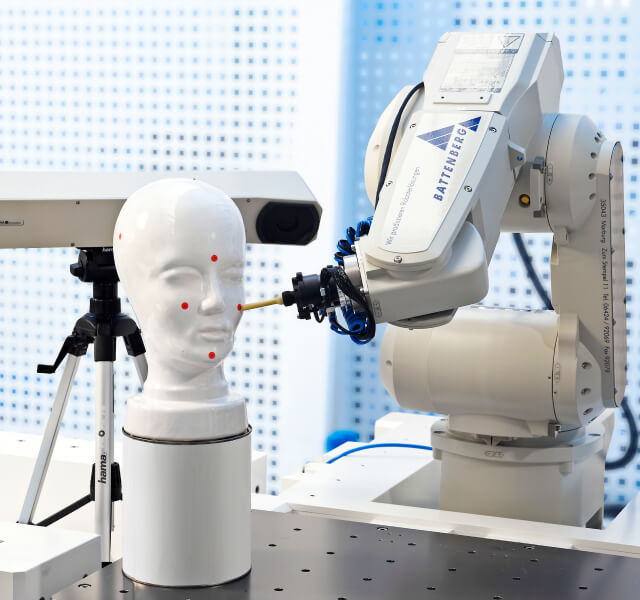
Medical
In order to meet quality and functionality standards, medical devices are subject to strict conformity assessments. The Battenberg Robotic Measuring is used to validate functional tests.
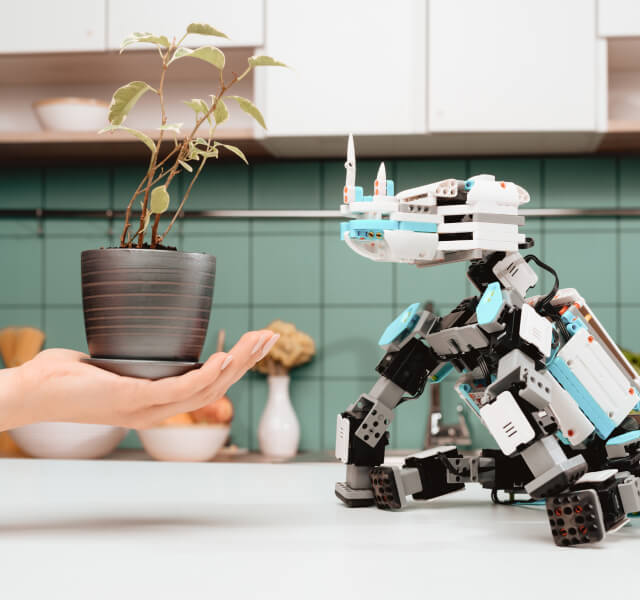
Lifestyle
The determination of functional haptic and optical reviews of lifestyle products by physical measurement variables is the task of Battenberg Robotic Measuring.
Reference customers
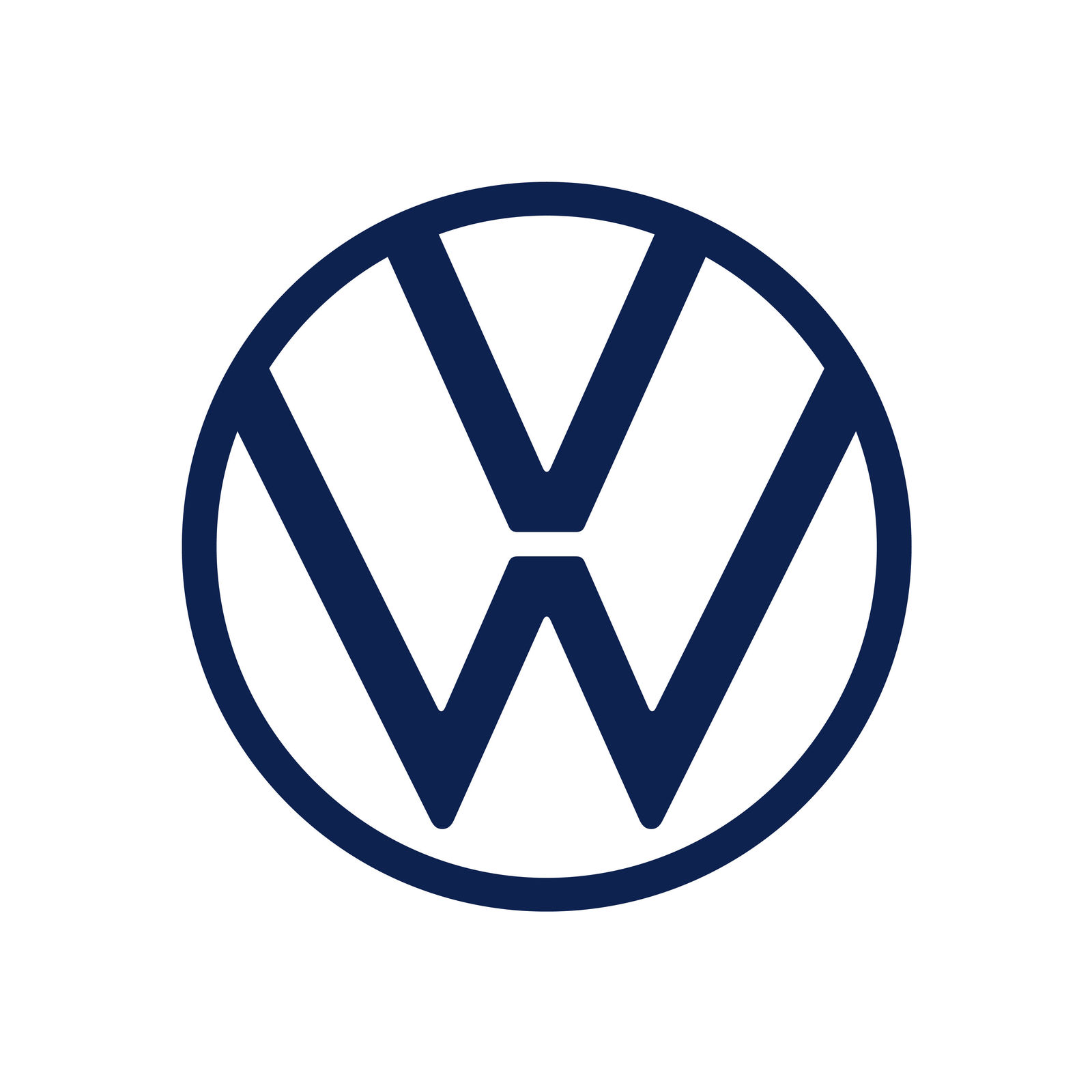
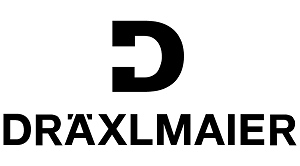
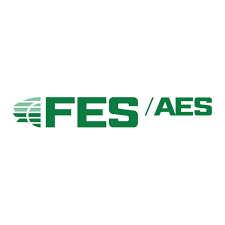
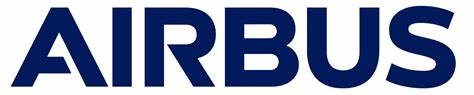

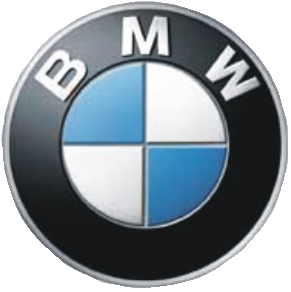
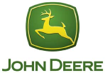
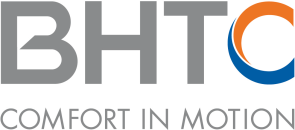
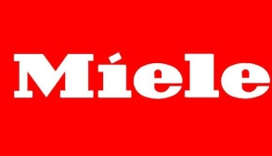

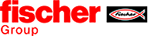
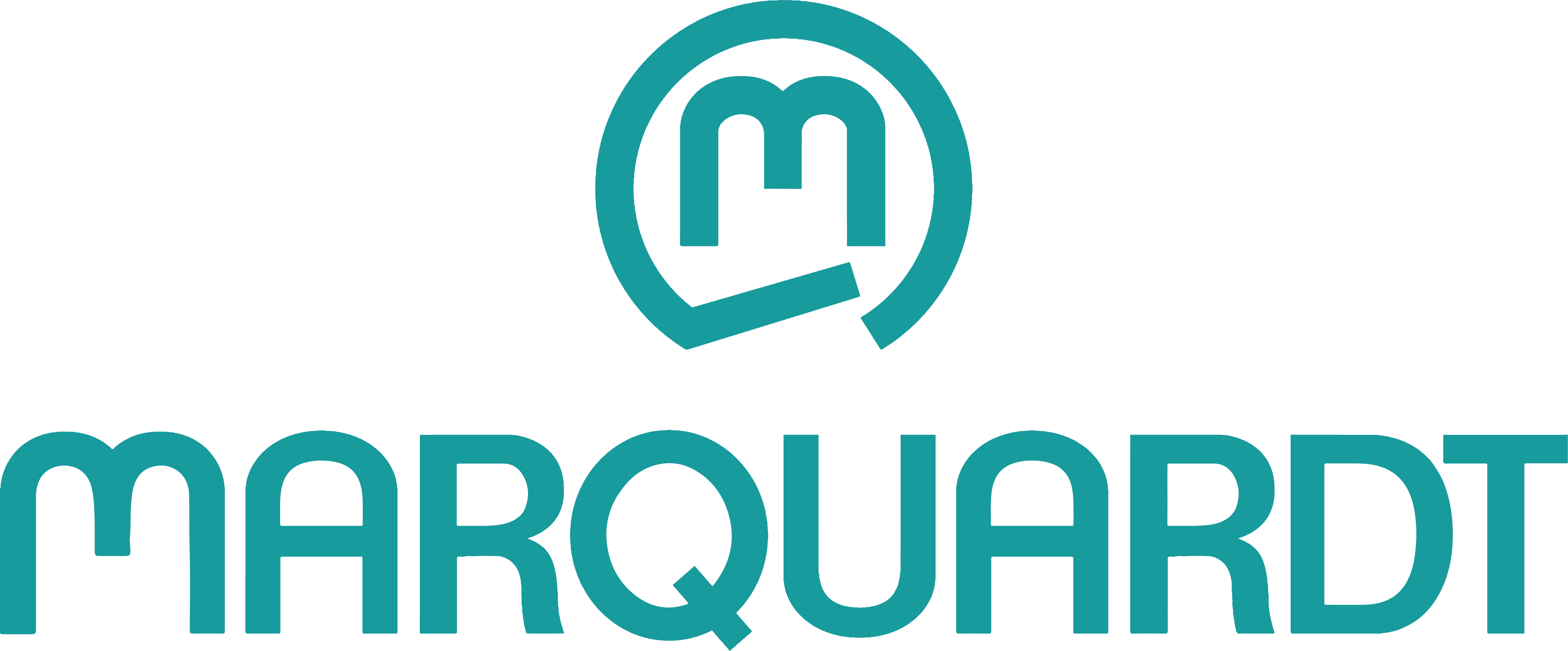
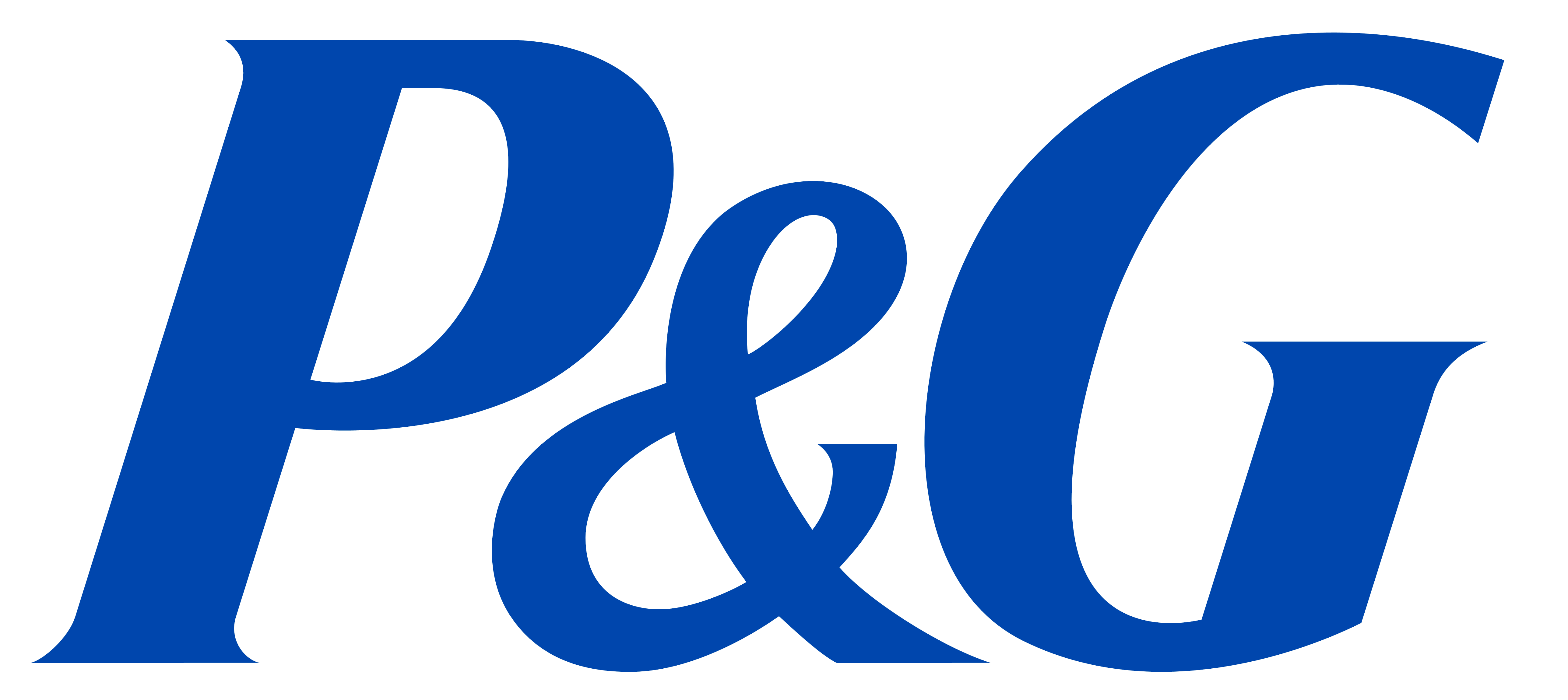
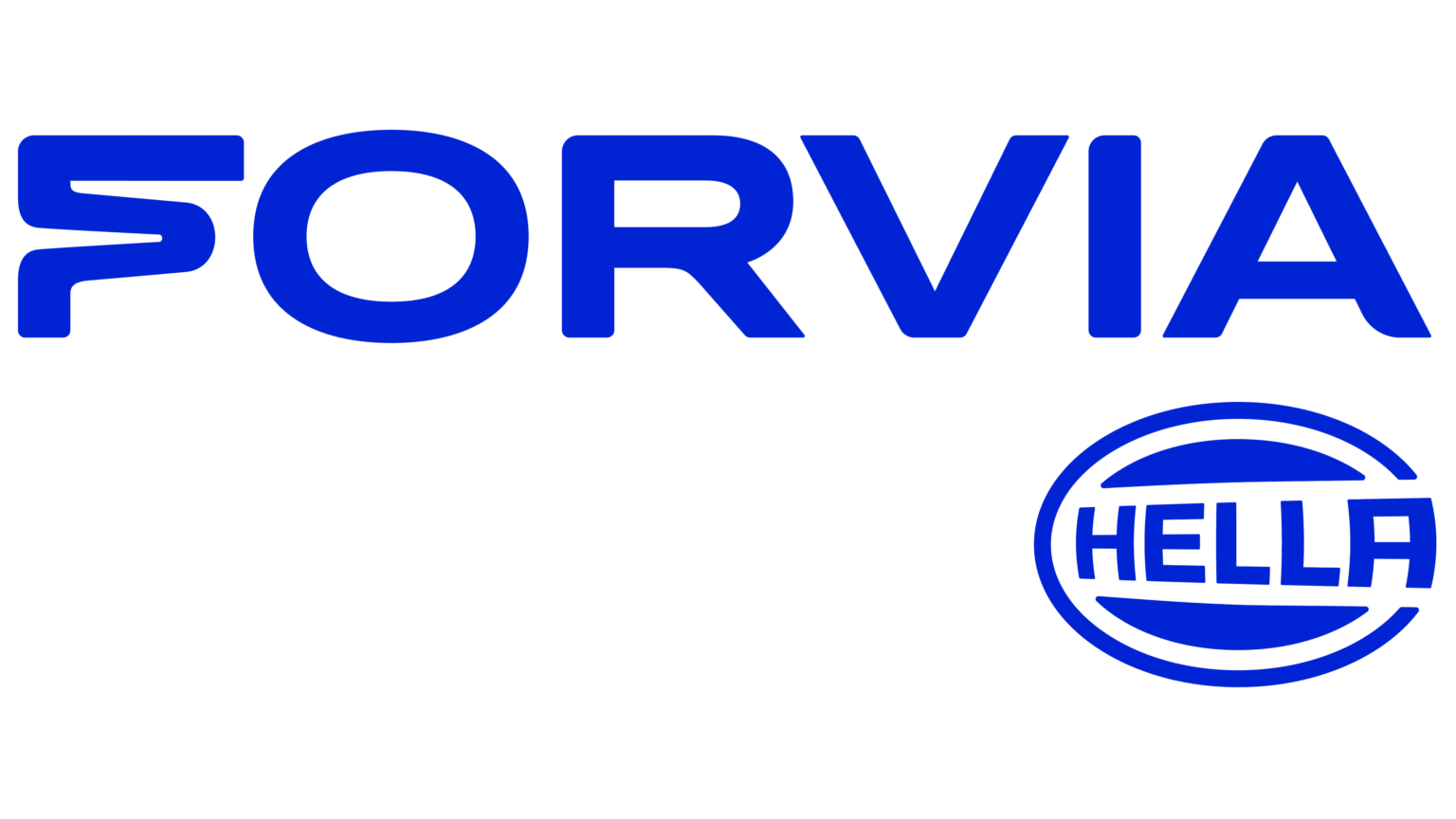


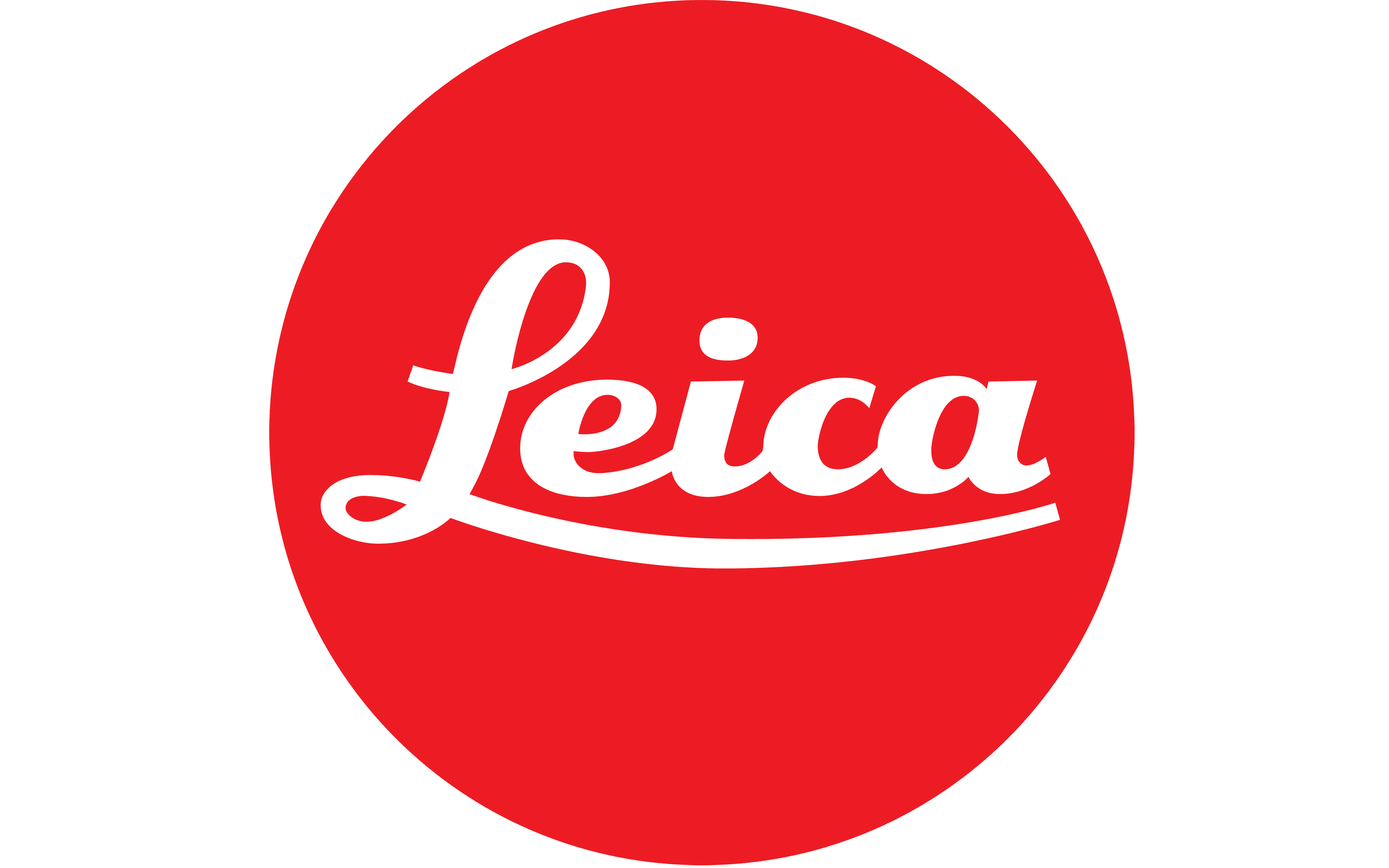
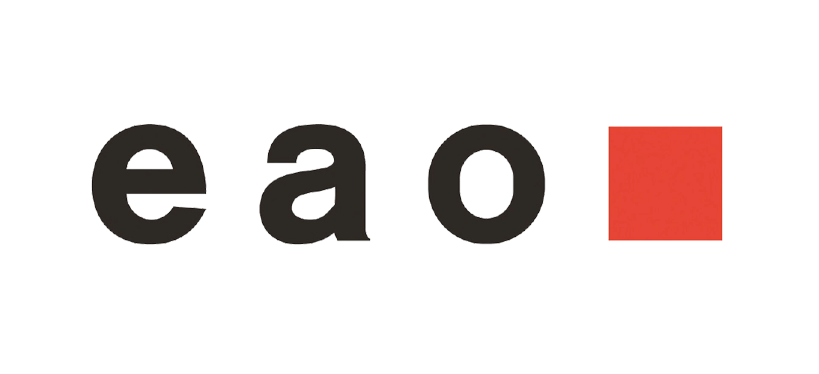
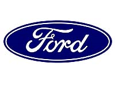
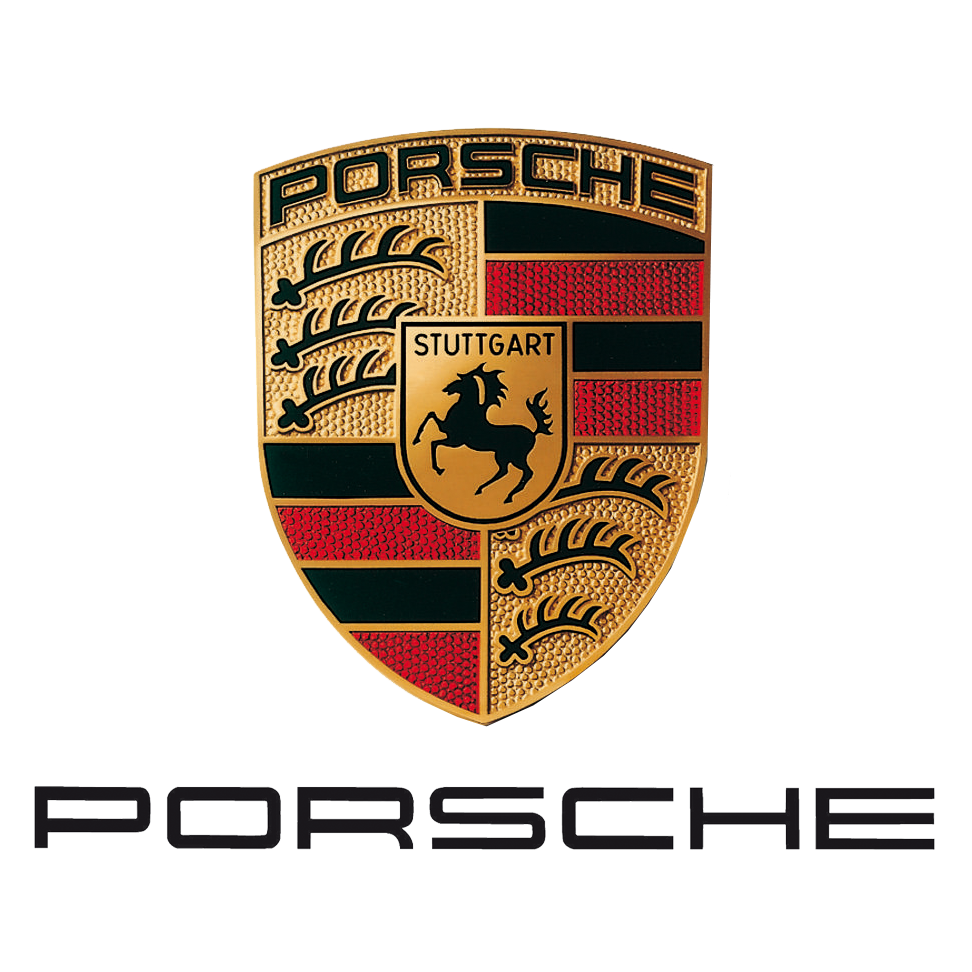
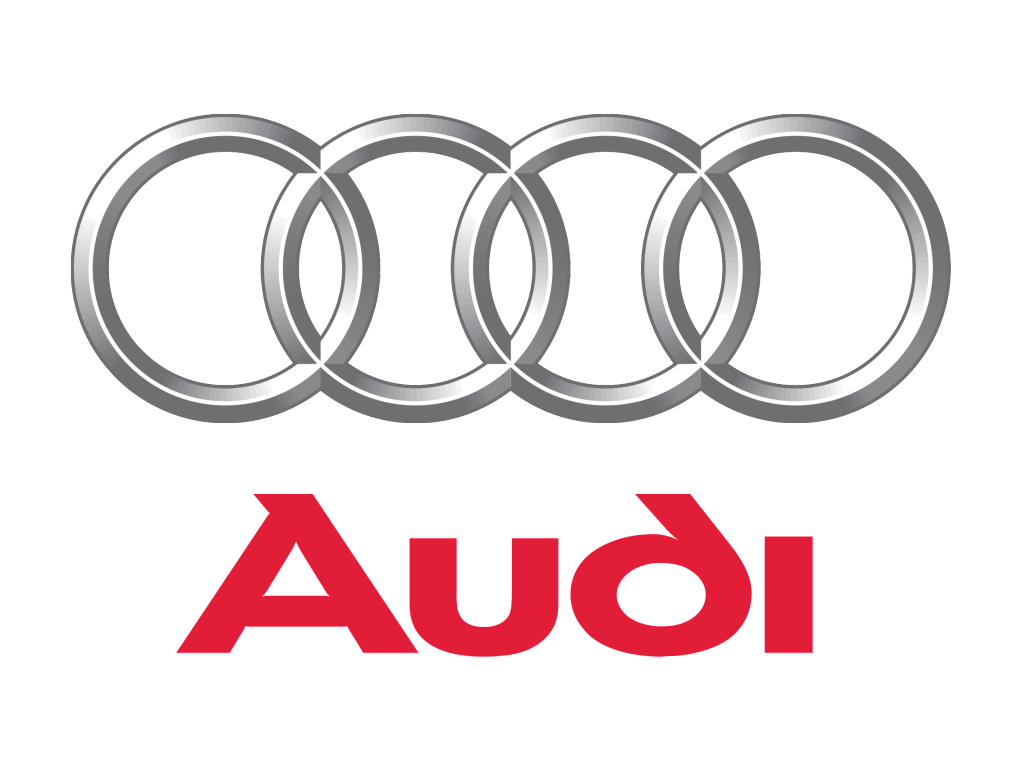
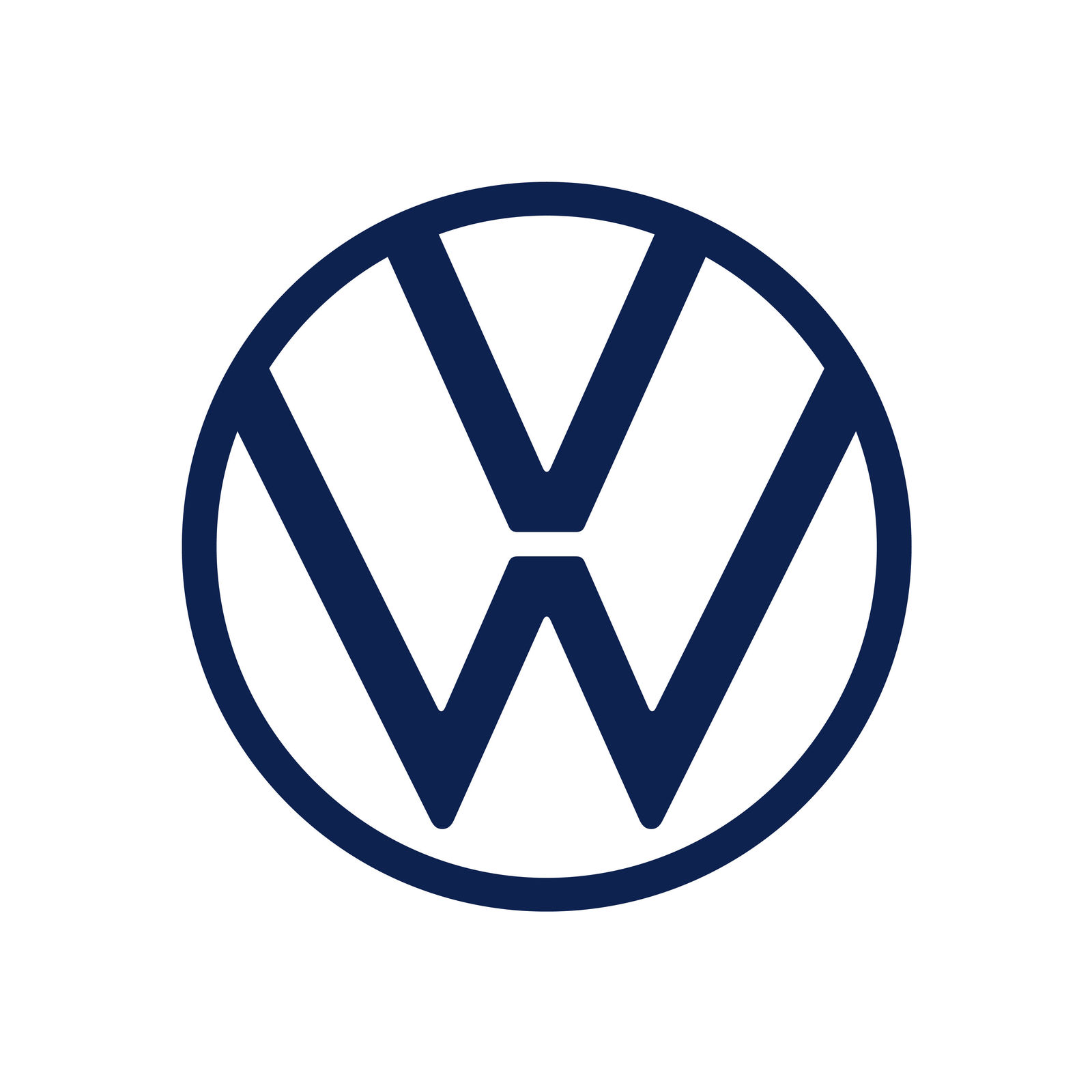
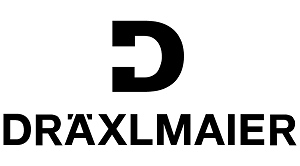
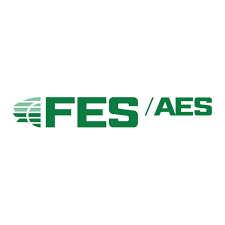
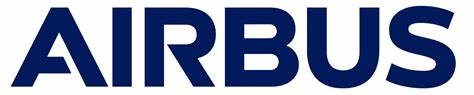


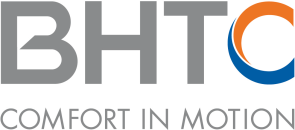
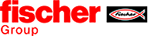
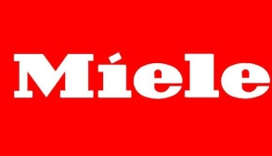
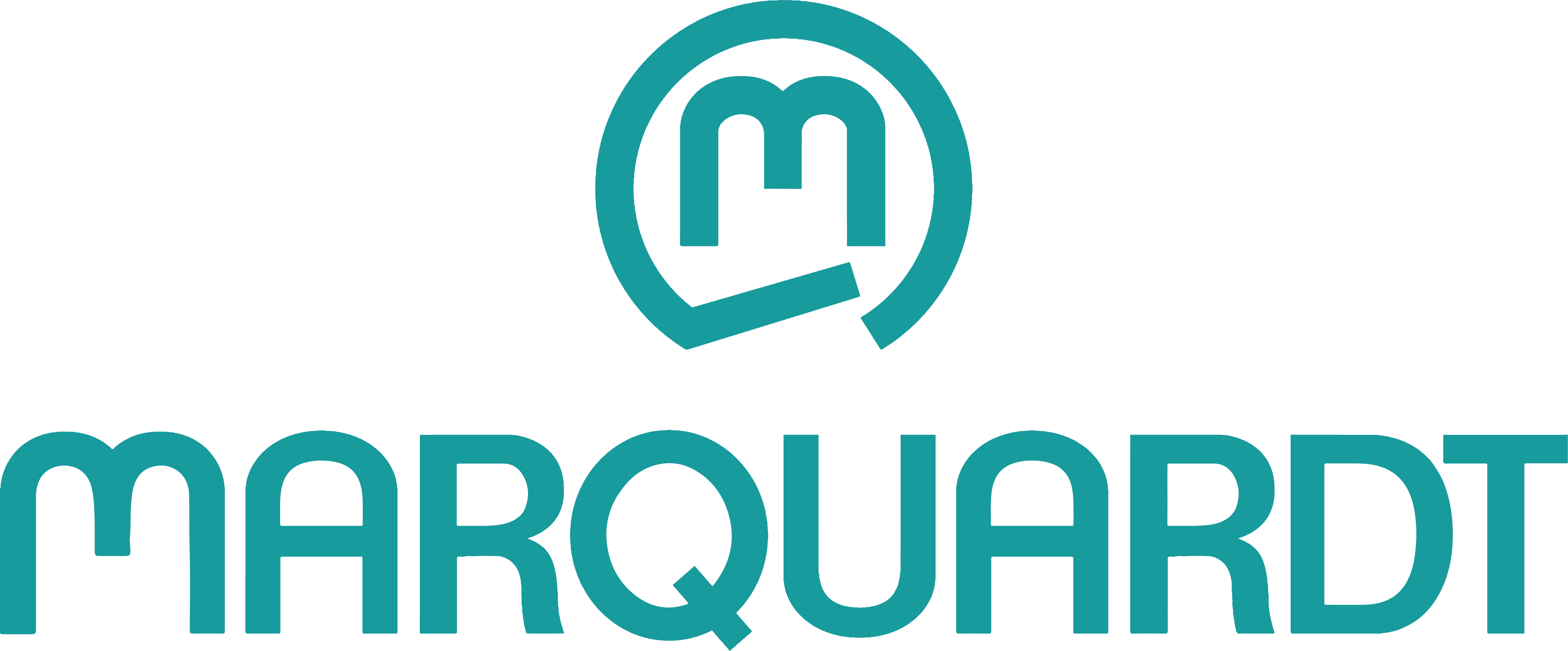
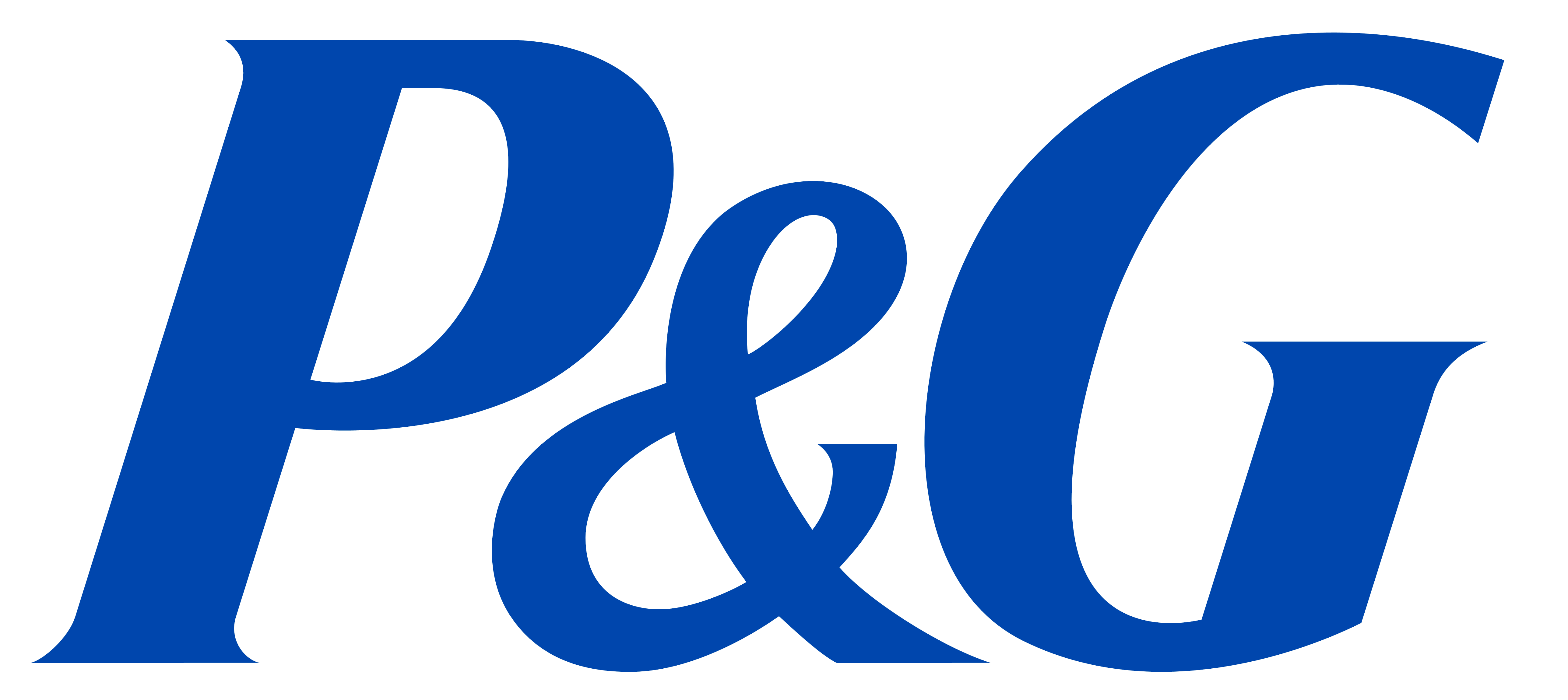
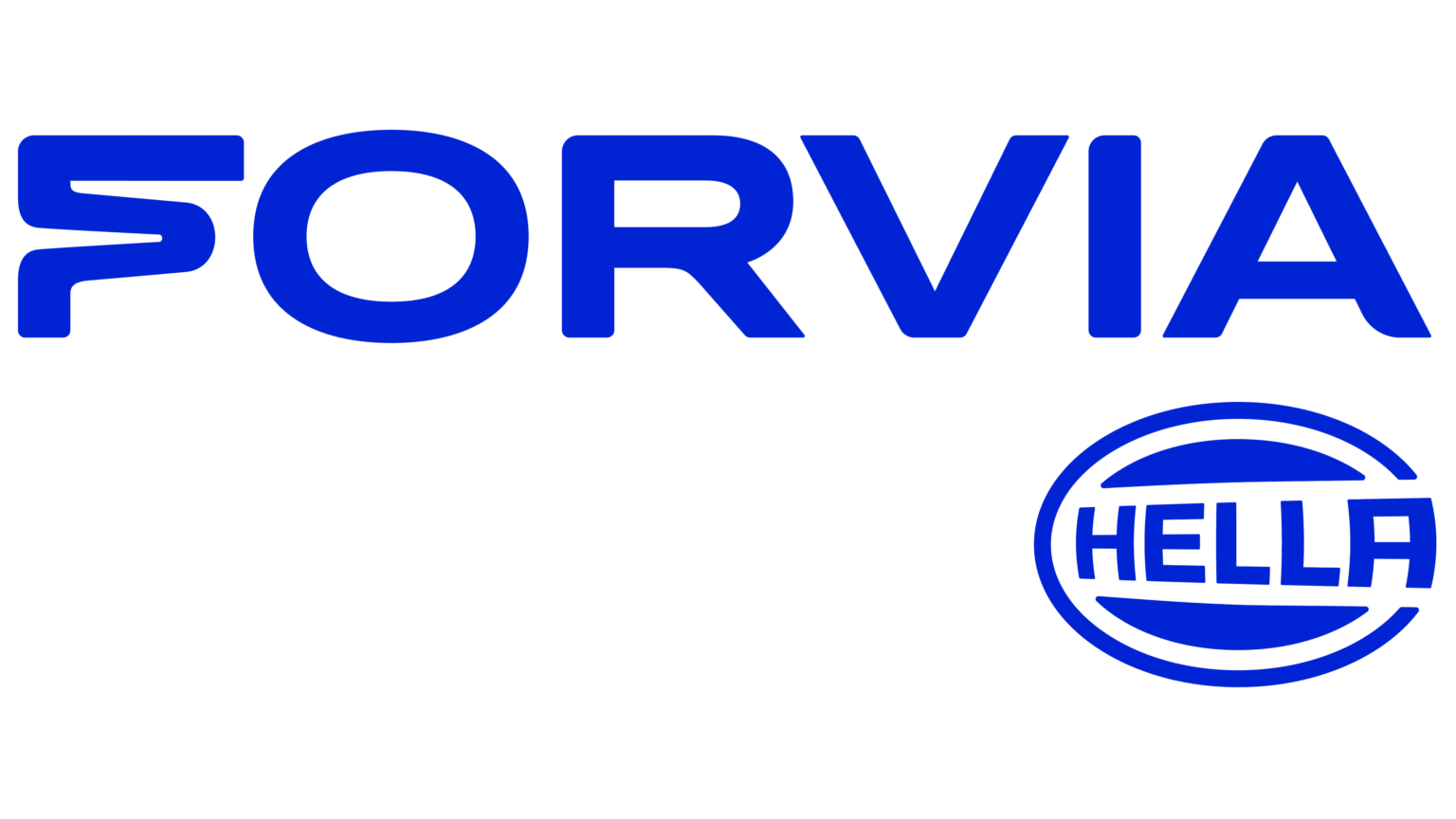
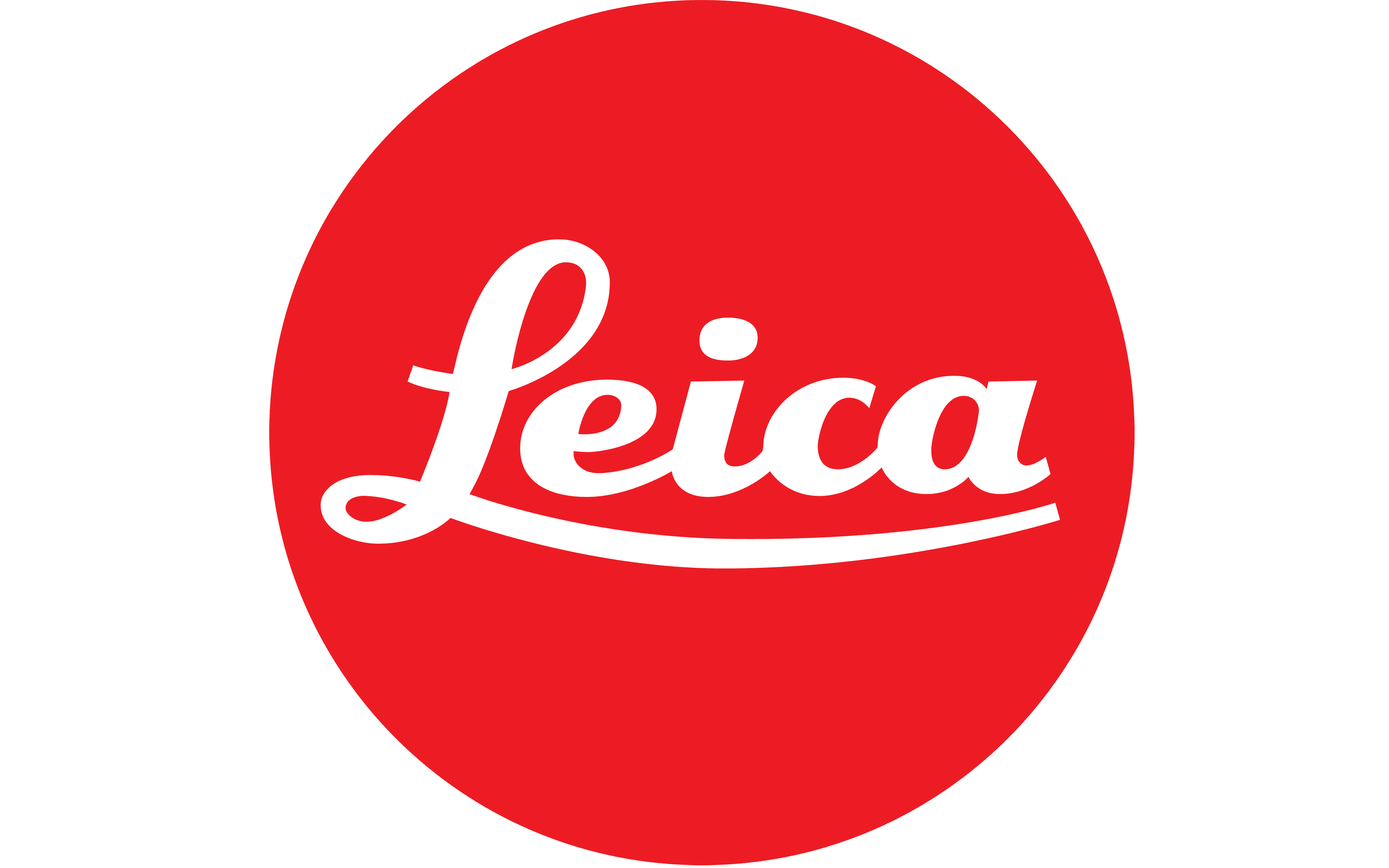
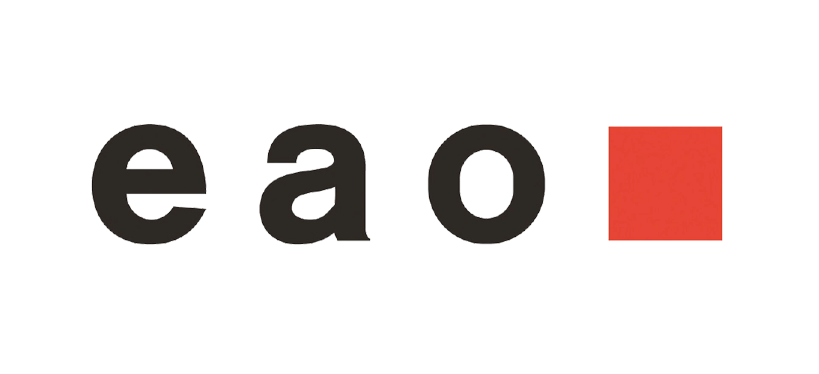
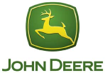

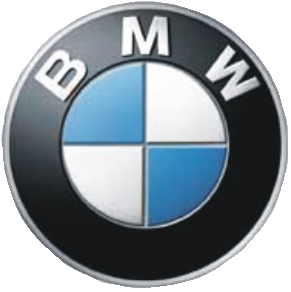

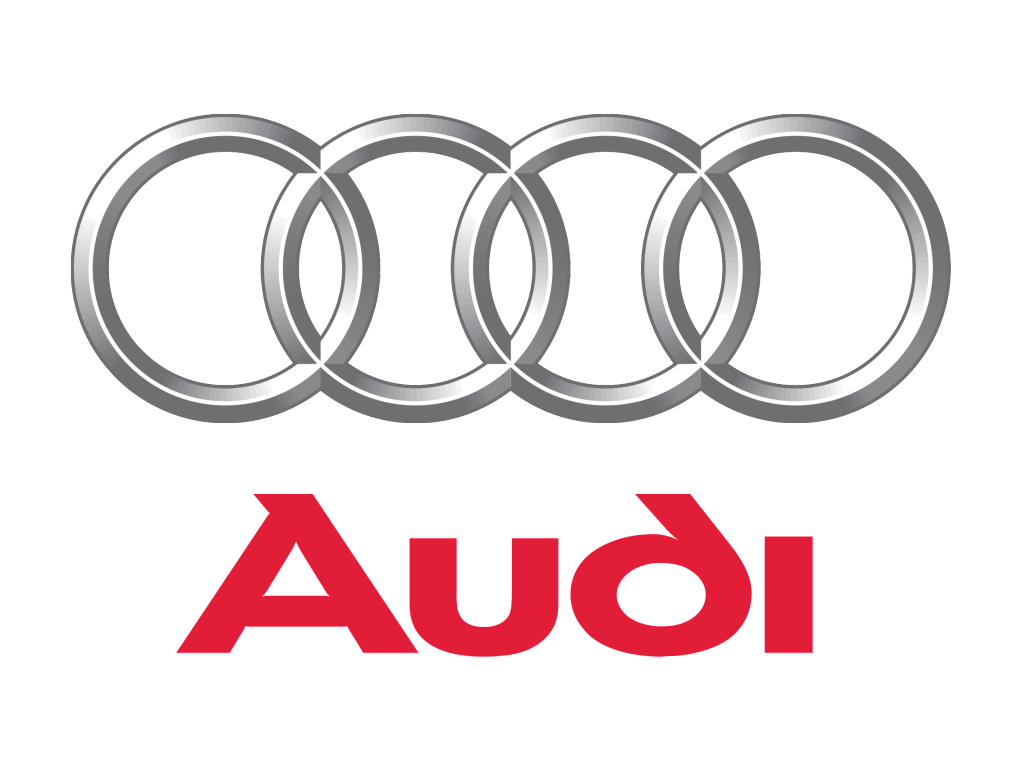
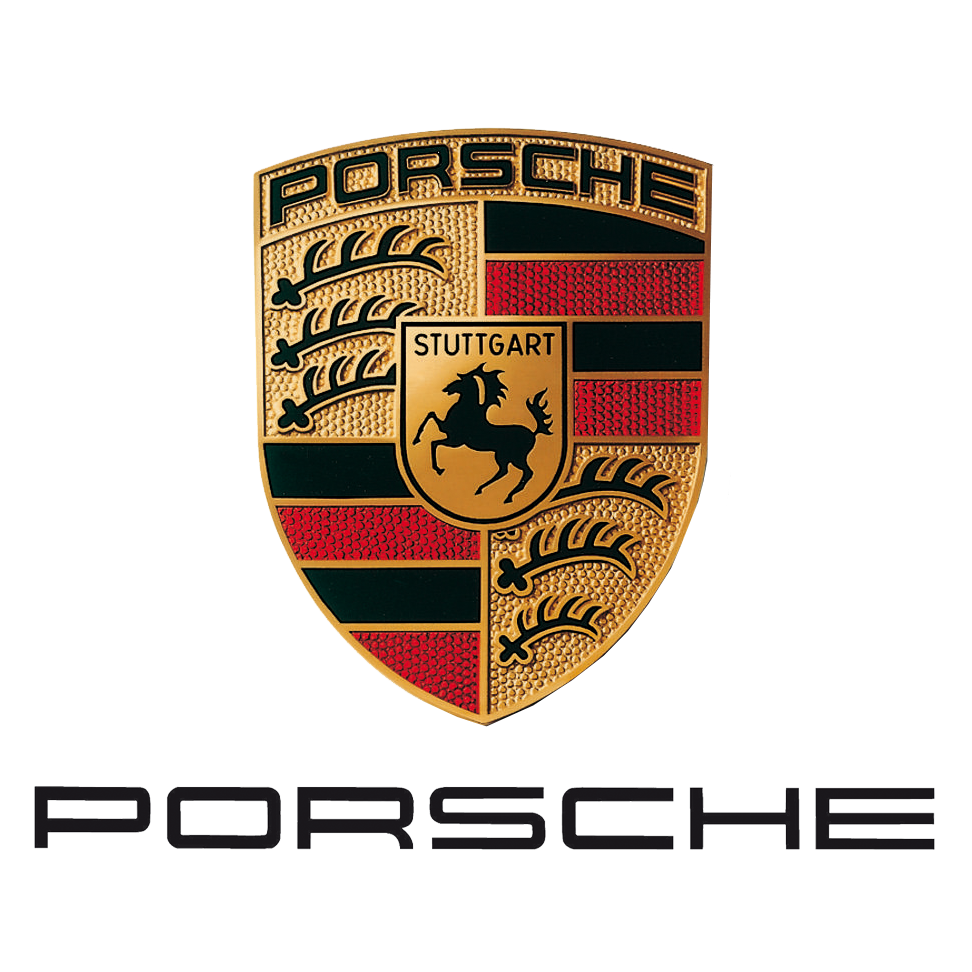
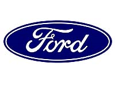